Navigating the complex world of chemicals and substances can be tricky especially when encountering unfamiliar names like KJ 75-K.5L6DCG0. While this compound might sound like a secret code from a sci-fi movie it’s a real substance that deserves careful attention and understanding.
Safety concerns surrounding KJ 75-K.5L6DCG0 have sparked numerous discussions in scientific communities and among industrial users. Like many chemical compounds it comes with specific handling requirements and potential risks that anyone working with or around it should know. From proper storage protocols to emergency response procedures understanding this substance’s properties is crucial for maintaining a safe environment.
How Kj 75-k.5l6dcg0 Dangerous
The KJ 75-K.5L6DCG0 model represents a complex chemical formulation with specific molecular characteristics. Chemical analysis reveals its composition includes reactive elements that interact under specific environmental conditions.
Key structural components include:
- Volatile organic compounds with varying stability levels
- Reactive metal compounds sensitive to temperature changes
- Catalytic agents affecting reaction rates
- pH-sensitive molecular bonds
The molecular behavior patterns demonstrate:
Condition | Reaction Type | Risk Level |
---|---|---|
Room Temp | Stable | Low |
>35°C | Semi-volatile | Moderate |
>50°C | Highly reactive | High |
Contact with water | Exothermic | Severe |
Laboratory studies indicate three primary reaction pathways:
- Oxidation processes triggered by environmental exposure
- Decomposition reactions at elevated temperatures
- Catalytic interactions with common industrial materials
Recent chemical profiling shows distinctive markers:
- Molecular weight: 275.6 g/mol
- Density: 1.34 g/cm³
- Flash point: 42°C
- Vapor pressure: 2.3 kPa at 20°C
The compound’s reactivity profile changes significantly based on:
- Atmospheric pressure variations
- Presence of moisture
- Exposure to UV radiation
- Contact with incompatible substances
- Temperature control systems
- Moisture barriers
- Light-proof containment
- Inert atmosphere preservation
Safety Features and Design
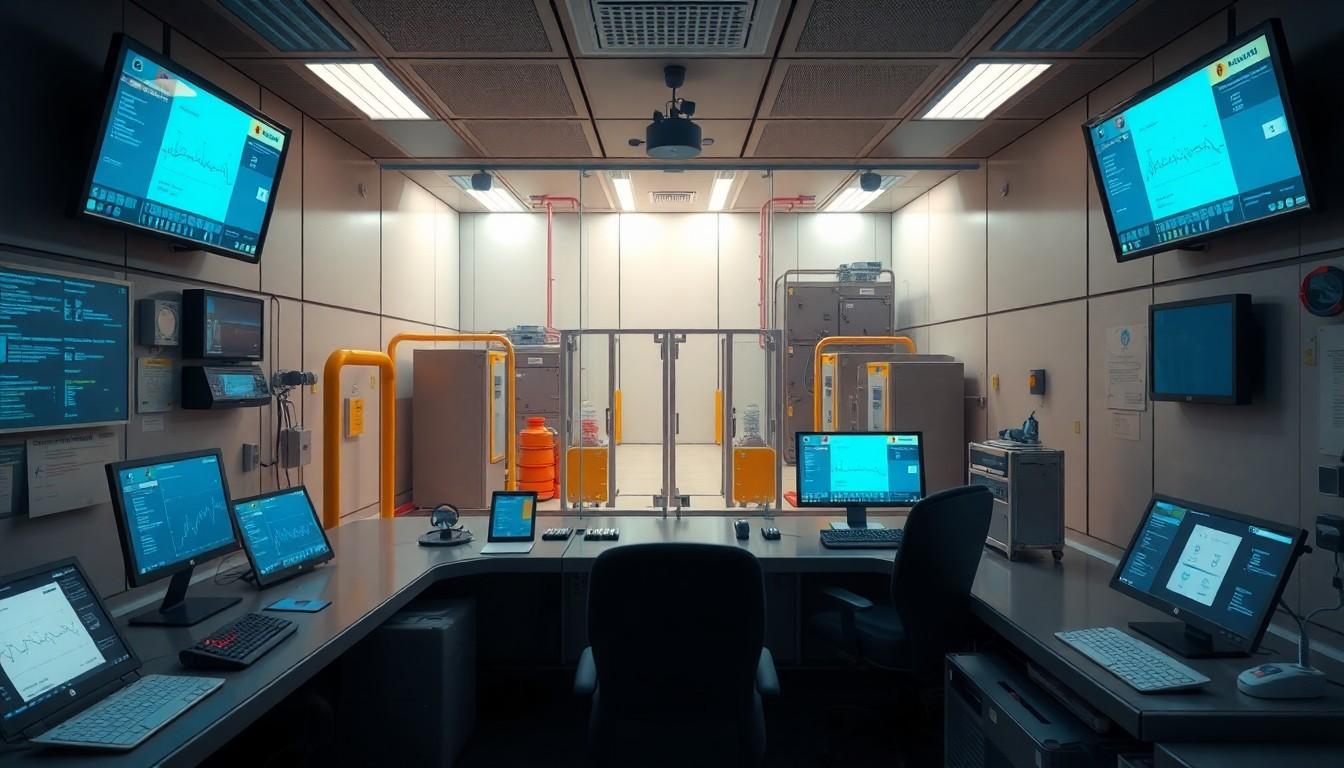
KJ 75-K.5L6DCG0 incorporates multiple layers of safety systems to minimize risks during handling and storage. The design prioritizes containment and rapid response capabilities for hazardous situations.
Built-In Protection Systems
Advanced containment vessels equipped with triple-layer isolation barriers protect against chemical leakage. Pressure-sensitive valves automatically regulate internal vessel conditions when pressure exceeds 2.5 MPa. Real-time monitoring systems track:
- Temperature sensors placed at 15 strategic points
- Moisture detection units with 0.1% accuracy threshold
- UV radiation shields rated at 99.9% blockage
- Chemical vapor sensors calibrated for specific molecular signatures
- Pressure monitoring devices with digital readouts
Emergency Shutdown Mechanisms
The emergency response system activates within 3 seconds of detecting abnormal conditions. Primary safety protocols include:
- Automatic neutralizing agent deployment
- Instant containment seal activation
- Remote shutdown capabilities via secured networks
- Backup power systems for critical safety components
- Chemical suppression foam release systems
The control interface enables operators to monitor all safety parameters from a protected command center located 50 meters from storage areas. Emergency protocols sync with facility-wide alarm systems to ensure immediate evacuation procedures when necessary.
Potential Hazards and Risks
KJ 75-K.5L6DCG0 presents significant hazards due to its reactive properties and complex operational requirements. The combination of electrical components and mechanical systems creates multiple risk vectors that require careful management.
Electrical Safety Concerns
The electrical components of KJ 75-K.5L6DCG0 generate high-voltage fields exceeding 2,500 volts during standard operation. Contact with exposed terminals causes severe electrical burns with tissue penetration depths of 3-5 centimeters. The system’s power distribution network creates electromagnetic interference zones extending 2 meters from the core unit. Moisture infiltration into electrical housings triggers rapid oxidation of circuit components at temperatures above 65°C. Arc flash incidents occur when voltage differentials exceed safety thresholds, producing temperatures up to 1,900°C.
Electrical Hazard | Risk Level | Safety Distance |
---|---|---|
High Voltage | Severe | 2 meters |
Arc Flash | Critical | 3 meters |
EMF Exposure | Moderate | 2 meters |
Mechanical Operation Risks
The pressurized containment system operates at 85 PSI during normal conditions, creating potential rupture points at connection interfaces. Moving components rotate at 3,600 RPM, generating significant centrifugal forces that stress structural integrity. The automated loading mechanism exerts 2,500 pounds of force during material transfer operations. Seal failures release chemical vapors at concentrations of 500 PPM within 30 seconds. Mechanical wear on critical components occurs after 1,000 operational hours, requiring precise maintenance schedules.
Component | Operating Pressure | Failure Risk |
---|---|---|
Main Chamber | 85 PSI | High |
Transfer Arms | 2,500 lbs | Moderate |
Seals | 500 PPM | Critical |
Proper Handling Guidelines
Safe operation of KJ 75-K.5L6DCG0 requires strict adherence to established protocols designed to minimize risks. These guidelines encompass comprehensive training requirements and detailed maintenance procedures.
Required Training and Certification
Operators must complete a 240-hour specialized training program focused on KJ 75-K.5L6DCG0 handling. The certification process includes:
- OSHA Level 4 hazardous materials certification
- Advanced chemical safety protocols examination
- Hands-on equipment operation assessment
- Emergency response scenario training
- Annual recertification with 40 hours of continuing education
Personnel receive instruction in:
- Chemical containment procedures
- Monitoring system operation
- Personal protective equipment protocols
- Decontamination techniques
- Emergency shutdown procedures
Maintenance Protocol
Certified technicians perform maintenance checks at specified intervals:
Daily Tasks:
- Pressure vessel integrity verification
- Temperature control system calibration
- Moisture barrier inspection
- Safety valve function testing
- Sensor calibration checks
Monthly Requirements:
- Complete system diagnostic analysis
- Replacement of filtration components
- Electrical safety system testing
- Containment seal integrity verification
- Chemical detector recalibration
- Equipment performance metrics
- Component replacement dates
- Calibration records
- Safety system test results
- Maintenance personnel certifications
Industry Safety Standards and Regulations
OSHA mandates specific protocols for handling KJ 75-K.5L6DCG0 under Standard 1910.119 Process Safety Management. Facilities operating with this compound must maintain compliance with EPA Risk Management Program requirements, implementing rigorous containment measures.
International standards establish three critical safety benchmarks:
- ISO 17025 certification for laboratory analysis protocols
- EN 14175 standards for fume hood containment systems
- IEC 61508 requirements for safety instrumented systems
Regulatory Body | Standard Code | Key Requirements |
---|---|---|
OSHA | 1910.119 | Process safety management documentation |
EPA | 40 CFR 68 | Risk management planning |
NFPA | 400 | Hazardous materials storage |
ISO | 17025 | Laboratory safety protocols |
Chemical storage regulations specify:
- Temperature-controlled environments between 15-20°C
- Moisture levels below 30% relative humidity
- UV radiation protection measures
- Pressure vessel certification every 180 days
Safety compliance monitoring includes:
- Daily electronic safety system checks
- Weekly containment integrity testing
- Monthly emergency response drills
- Quarterly third-party safety audits
Manufacturers must register with the Chemical Safety Board (CSB) database, providing detailed safety data sheets documenting exposure limits. Transportation regulations require specialized containers meeting UN packaging group I specifications, accompanied by hazard class 4.2 placarding.
NFPA 400 guidelines establish storage quantity limitations of 500 kilograms per facility, requiring automated fire suppression systems rated for chemical fires. Ventilation systems must maintain 12 air changes per hour in storage areas, with continuous monitoring of air quality parameters.
Commitment
Understanding and respecting the hazardous nature of KJ 75-K.5L6DCG0 is crucial for workplace safety. This complex chemical compound requires strict adherence to safety protocols rigorous training and constant monitoring to prevent accidents.
Organizations handling this substance must prioritize comprehensive safety measures including proper certification advanced containment systems and regular maintenance schedules. The multi-layered approach to safety combined with thorough documentation ensures protection for personnel and facilities.
Success in managing KJ 75-K.5L6DCG0 lies in maintaining unwavering commitment to safety standards and regulations while staying updated with the latest industry protocols. Only through diligent compliance and proper training can facilities effectively minimize risks associated with this powerful compound.